For over 30 pioneering years, majestic winged Space Shuttles rocketed to orbit, captivating the world before their retirement in 2011. But what exactly was this iconic spacecraft trio capable of? How did the Shuttle system advance in space operations and exploration, and what made it a revolutionary design? What is Space Shuttle, first of all?
In this exploration, we dive into the groundbreaking Shuttle program’s achievements and limitations. We examine the advanced functions allowing astronauts to live and conduct cutting-edge microgravity research at lengths in low Earth orbit.
Examine standout missions that deployed probes across our solar system, built the International Space Station, and demonstrated both the promise and challenges of reusable spacecraft. From main engines to thermal tiles, orbital maneuvering to detecting and repairs, discover what’s behind this engineering feat known as the Space Shuttle.
Learn how bold innovations drove spaceflight to new heights, even amidst heartbreaks. Let us reflect on the Shuttle era’s legacy carrying over to propel future ventures as we question what is Space Shuttle.
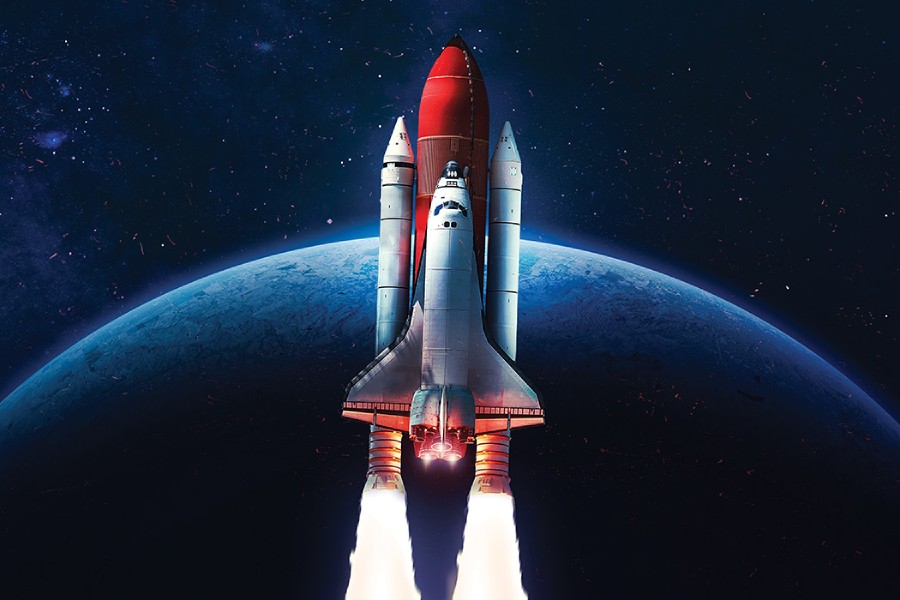
What Is Space Shuttle?
So, what is Space Shuttle? The Space Shuttle, officially called the Space Transportation System (STS), refers to the partially reusable spacecraft system operated by NASA from 1981 to 2011.
It consisted of the winged shuttle orbiter vehicle, twin solid rocket boosters that provided the main thrust, and an expendable external tank holding liquid fuel.
Space shuttles launched vertically like a rocket, powered by the three components working in unison. Once in low Earth orbit, Shuttle capabilities included deploying satellites, ferrying cargo and supplies, and housing crews of up to eight astronauts for missions typically lasting around two weeks.
The orbiter component was designed to re-enter the atmosphere gliding to a runway and landing under pilot control, making the Space Shuttle the first partially reusable spacecraft. Five orbiters were built over the program’s duration before retirement in 2011 after 135 missions.
Space Shuttle Capabilities
Reusable spacecraft design
The signature leap forward enabled by the shuttle system design was a partially reusable spacecraft architecture for economical and regular access to orbit. While the large External Tanks were expended on each flight.
The Orbiter vehicle and twin Solid Rocket Boosters could be refurbished for reuse after launch and recovery, reducing per-mission costs. This reusability allowed the versatile shuttles to not only transport astronauts into low Earth orbit for weeks at a time across the construction of the International Space Station, but also loft diverse classified and science satellite payloads. The shuttle fleet had specialized thermal protection tiles and reinforced airframe structures.
This additional design enabled the vehicles to safely withstand the intense heat and forces of atmospheric reentry. It allowed them to conclude missions with piloted glide landings on runways.
Supporting satellite deploy and space station construction
While in orbit, the Space Shuttle’s capabilities included deploying interplanetary probes, research satellites, and defense spacecraft in diverse configurations tailored to each payload. The voluminous payload bay, robotic Canadarm grappler, and abundant power delivery facilitated rapid satellite deployments.
The Space Shuttle’s specialized capabilities enabled satellite deployments not feasible with conventional rockets alone. Additionally, the Shuttle’s vast cargo-carrying abilities and human spaceflight capacities prove pivotal in constructing the International Space Station (ISS).
By ferrying massive module components to orbit over four decades of assembly flights, the Space Shuttle was instrumental in building this multinational orbital complex.
Without the Shuttle fleet’s unique duo of heavy lift capacity combined with human orbital habitation, the expansive, football field-sized ISS could never have been constructed. This construction was only made possible by ferrying oversized station modules, truss segments, and international crews using the shuttle fleet.
Evolution and Design
Historical background
The Space Shuttle originated in designs from the 1960s seeking reusability to reduce space access costs. NASA sought a replacement vehicle for the limited Apollo spacecraft. NASA funded multiple early Shuttle concept studies before budget impacts led Congress to approve development funding in 1972.
Critical early architectural decisions included the selection of a two-stage winged orbiter launch profile as well as fragile tile-based thermal protections to withstand reentry heating.
Many additional innovations in materials, avionics, and simulations developed throughout the 1970s. This continued until the first launch of orbiter Columbia in 1981, which inaugurated the program span.
Distinctive design elements
The Space Shuttle system integrated three main rocket-based components to achieve orbit. The winged orbiter vehicle contained the crew compartment and a large internal cargo bay equipped with the Canadarm robot manipulator arm.
Twin solid rocket boosters mounted on the external tank provided most of the initial thrust at launch prior to separation by parachute for recovery. The large external tank carried liquid oxygen and hydrogen fuel to supply the orbital maneuvering engines during the ascent to orbit.
Complex interactions between various factors made Space Shuttle missions possible. Precise propulsion delivery, aerodynamic forces, and advanced lightweight materials were important factors. Integrated avionics systems were another key enabling element.
These complex factors combined to make launches, orbital operations, and reentries feasible for the Space Shuttle while operating within strict performance constraints.
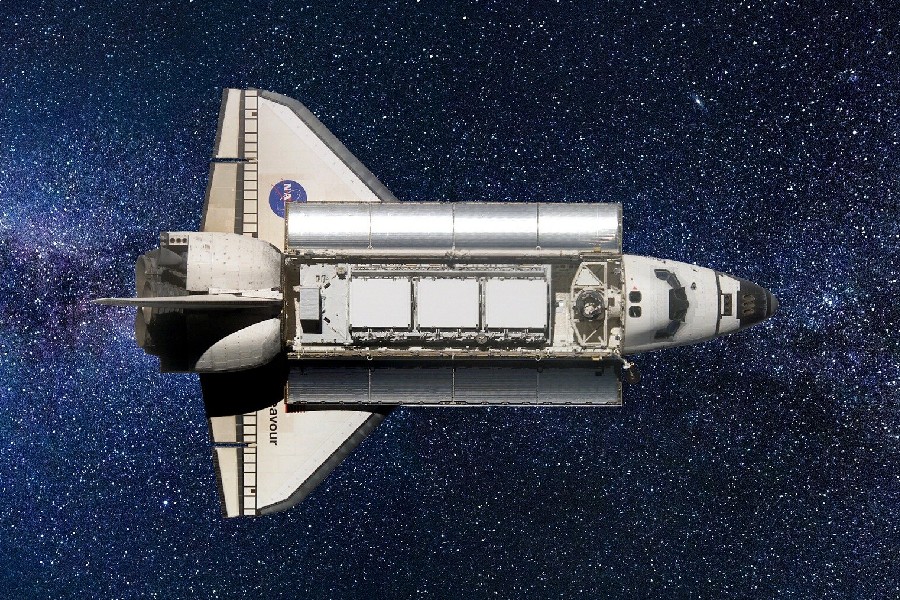
Components
Solid rocket boosters (SRBs)
Two solid rocket boosters gave the main thrust for the first two shuttle launch minutes. They contained solid propellant and nozzles to steer and provided 80% of the total lift-off thrust.
The boosters were then separated by small explosive charges and descended by parachutes for ocean recovery. After refurbishment following each use, the reusable SRBs were critical for enabling the shuttle’s heavy payload capacity.
External tank (ET)
The external tank held liquid oxygen and hydrogen to fuel the orbiter’s engines during ascent. After draining its propellants, the tank was discarded – the only non-reusable major Shuttle element. The tank consisted of a strong, lightweight aluminum exterior shell.
Its interior contained separate storage tanks for the fuels plus connected feedlines. It was sprayed with insulation foam, however the vulnerable foam posed a hazard that would be highlighted in later Shuttle accidents.
Orbiter vehicle (OV)
The Space Shuttle orbiter was the heart of the system. Being about the size of a DC-9 jet, it contained a payload bay for satellites or space station modules and a crew compartment for up to seven astronauts.
The orbiter also had three powerful rocket engines for propulsion, smaller maneuvering thrusters, and heat-radiating panels. Its distinctive swept-back delta wings enabled the crossover design from space to air flight vehicles. Advanced thermal protection tiles lining the underside dissipated the intense heat of re-entry.
Crew compartment
Housed astronauts on mission
The two-level pressurized crew compartment held up to eight astronauts while in orbit. It included shirt sleeve living quarters with storage plus controls and displays for maneuvering the orbiter.
It also contained a docking hatch and airlock for spacewalks or linking with space stations. Designed for a comfortable habitat, it had independent life support systems to allow extended orbital stays.
Safety equipment
Redundant systems enhanced crew safety, given the risky launch and re-entry conditions. These included backup flight computers and underfloor life rafts for emergency water ditchings.
Escape pole canisters held parachutes as contingency options for runway exit. Tragically, the safety equipment imperfections were proven by two mission losses.
Ceramic tiles
Withstood intense heating
The orbiter needed protection from extreme temperatures up to 2,900°F (1,600°C) during intense atmospheric reentry friction. Its thermal protection system used ceramic tiles containing fused silica glass and amorphous silicon dioxide able to withstand heat. Tens of thousands of individually fitted tiles covered the orbiter base and wings.
Laborious maintenance
Each tile is precisely shaped for required smoothness across orbiter skin. Fragile, easily damaged tiles underwent meticulous inspection and replacement between missions. Special bonding agents and felt strain isolators were used for attachment. Laborious upkeep issues overcome by reusable design.
Runway landing gear
Wheels and brakes
The landing gear included a nose wheel plus two main gear units with tires almost four feet tall. Advanced carbon brakes on the main wheels allowed tire smoke but a rapid deceleration from over 200 mph at touchdown. Interacting aerodynamic control surfaces also slowed vehicles on the runway.
Retracted in flight
Gear folding struts and side braces retracted the wheels into car-sized openings for stowage while the orbiter was in space, with doors keeping the bay aerodynamically smooth. Upon re-entry, redundant hydraulics lowered the landing gear for rollout stability after mission completion.
Rocket engines
Main engines
Three reusable Rocketdyne RS-25 liquid-fueled engines powered the orbiter after SRB separation, burning liquid oxygen and hydrogen drawn from the external tank.
Throttling between 65-109% of 375,000 pounds thrust, they were used to maneuver once on orbit after fuel depletion. The in-flight restartable engines also enabled abort options and relit to slow the vehicle upon re-entry after missions.
Attitude control
38 smaller liquid-fueled engines on the orbiter’s nose and aft fuselage provided precise attitude control in space. The thrusters fired in precise, quick pulses balanced around the orbiter’s mass balance point. This allowed using them to accomplish fine orbital maneuvering.
It also enabled performing smooth docking operations along the pitch, yaw, and roll axes while in space. These thrusters were critical for executing mission operations along all system flight regimes.
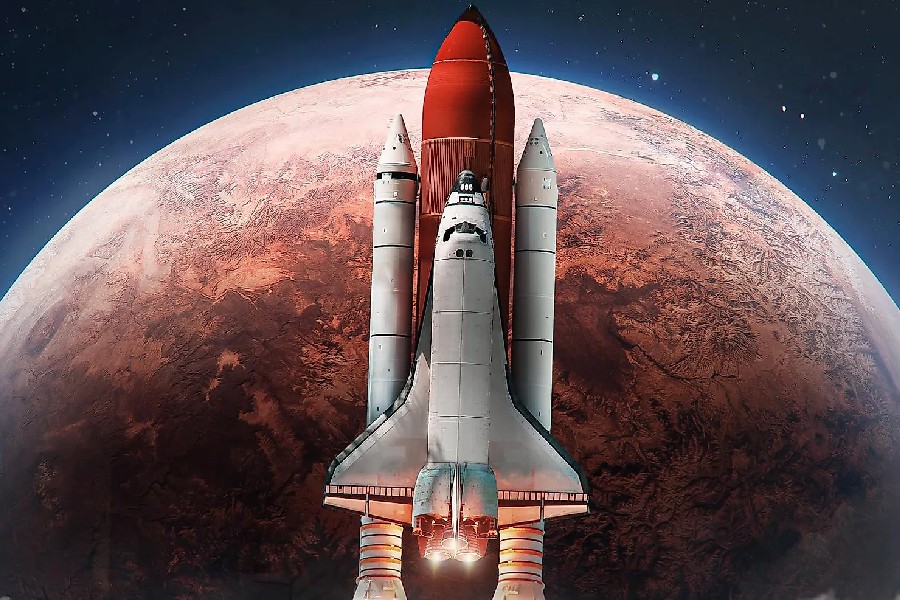
Launch of a Space Shuttle Mission
Preparation for launch
Extensive reviews and flight readiness tests were conducted months before launch. The external tank was then loaded with liquid oxygen and hydrogen propellants just prior to liftoff.
The astronauts boarded the orbiter several hours before launch when a closeout crew made final cabin checks. The hatch was sealed two hours before launch, and the vehicle soon switched to internal power. Precise countdown timing was critical for the launch.
Countdown to launch
As the countdown progressed, the orbiter switched to internal power and the access arm retracted around the two-hour mark. The hydrogen igniter activated for the main engine to start. At T-minus six seconds, the computers ignited the three RS-25 engines.
At the moment zero, the solid rocket boosters fired, with the hold-down bolts releasing as the call of “Liftoff! We have a liftoff!” sounded while the Shuttle cleared the tower within eight seconds. Pushed by the immense thrust, the crew was pushed back into their seats by up to three times the force of gravity.
Minutes after launch
After liftoff, the vehicle rolled in flight to align its trajectory with the desired insertion orbit, as the crew confirmed guidance tracking within minutes. The launch pad’s flame trench and movable flame deflector redirected exhaust plumes from the SRBs upwards.
SRB separation occurred two minutes into the flight, with the external fuel tank discarded eight minutes later as the orbiter engines were cut off, having successfully reached low Earth orbit.
Operations and Missions
Overview of mission types
While in orbit, Space Shuttle capabilities supported diverse operations across mission durations averaging nearly two weeks. Typical satellite deployment, planetary probe release and vehicle testing missions proceeded on a tighter 5-7 day timeline.
However, building the International Space Station required far longer efforts, with multiple flights needed to ferry key station modules, truss segments, resident crews and replenishment supplies.
Notable missions
Hubble Space Telescope servicing missions required meticulous astronaut extravehicular activities (EVAs). This includes complex spacewalks coordinated with the Space Shuttle’s robot arm and orbiter positioning over multiple intense mission days.
The riskiest ISS assembly flight, STS-114 in 2005, rigorously tested safety improvements after the Columbia tragedy, including debuting an experimental Orbiter Boom debris inspection system. It also wrung out new techniques like R-bar rotational approaches and demonstrated manned maneuvering unit spacewalks underneath the station structure.
Conclusion
The majestic Space Shuttle program represented an ambitious leap into reusable space transportation and expanding human spaceflight capabilities. We hope examining all facets of what is Space Shuttle and how it operated has deepened your appreciation of this winged spacecraft and the many pioneers who designed, built, and flew it during its 30-year tenure.
From audacious technological feats like deploying the Hubble Space Telescope to a lasting legacy grounded in cooperative space ventures and lessons purchased through tragedy, the shuttle era transformed access to orbit and left an indelible impact.
Though the fleet has since retired, new generations now build on the Shuttle’s achievements as humanity continues pushing outward. This overview has hopefully enhanced the understanding of what this one-of-a-kind vehicle accomplished for its era.